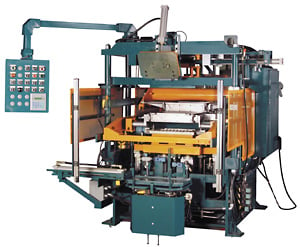
With the state-of-the-art Harrison flaskless matchplate mold machine, Buffalo Metal Casting has taken a major step forward in automated mold-making technology designed to boost productivity on behalf of its customers. System features and capabilities include:
Productivity Gains for our Customers
-
One operator can produce a mold every 40 seconds
-
Plate changes can be made in 60 seconds
-
Cores can be set while the cope is being made
-
Mold push-off can be done manually or automatically while the drag is being made
-
Adapted to our existing sand system and pour line
-
Existing patterns can be used 100 pattern programs stored in memory for quick call-up
-
Risers and chills can be set quickly and easily
-
More consistent mold quality provides predictable results
-
Consistent production improves delivery and increases capacity
System Capability and Flexibility for Customer Molds
-
Run jobs requiring anywhere from one mold up to dedicated continuous production
-
Special molding capability including contour molding, special peening, open risers, chills, and multiple sprue locations
-
Flask capacity to 14" x 22" - up to 6" over 8" with single closing pin system
-
Variable mold height - any combination up to the maximum flask capacity
-
Custom flask sizes can be used to suit existing patterns
-
Pattern height capacity to 4-1/2" from parting line
-
Recommended pattern plate thickness of 1" (without thin-pattern option)
-
Allen-Bradley PLC for reliability and flexible machine functions
-
Table impact vibrator for packing sand during the fill; pattern vibrator for mold stripping - manual or automatic
|